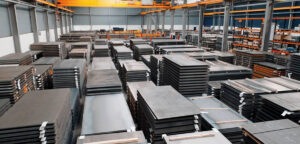
- The company
- Sustainability
- Assortment
- Pressure vessel steels
- Steels acc. ASTM/ASME standard
- HIC-resistant sheets
- Structural steels
- Weldable fine-grained structural steels
- Shipbuilding steels
- Offshore steels
- Sheet metal for line and construction pipes
- High-strength steels
- Wear-resistant steels
- Creusabro®
- toughcore®
- Quenched and tempered steels
- Case-hardening steels
- Ballistic Steels for civil applications
- Editing
- Service
- Industries
English
German